Honors Thesis
In conjunction with the development of the garments I developed my thesis focusing on the manufacturing needs to bring these products to market. I researched the wearable tech market, current manufacturing methods, and design theory. I then created documentation that fulfilled the identified needs to create a wearable tech product. I then used three of the garments to act as case studies for different forms of manufacturing.
Market Framework
This framework was developed for understanding the market, by product category, The x-axis represents the scale of form to function whereas the y-axis represents the use in regards to it being for an individual or the collective. The purpose of this graph is to allow innovators, companies, etc. to locate where their product falls in comparison to others.
There are eight main categories that products can fall under, shown as the headers on the graph. Each grouping is given a color, and to show that these are not rigid categories, the gradient was included.


Documentation Development
I developed documentation by updated standard apparel conventions to incorporate the electronic components. I began by updating the spec sheet, adding electronic information like schematics and codes. I then curated documentation in regards to sample and inventory organization as well as labeling and packaging rules. The key form of integration came in regards to the integrated tech flats and patterns. During this step, I developed a method for incorporating trace layouts into the fashion tech flat, then moving that information into a trace routing pattern and finally into a pattern for cutting on the factory floor.
Process Order
SKU

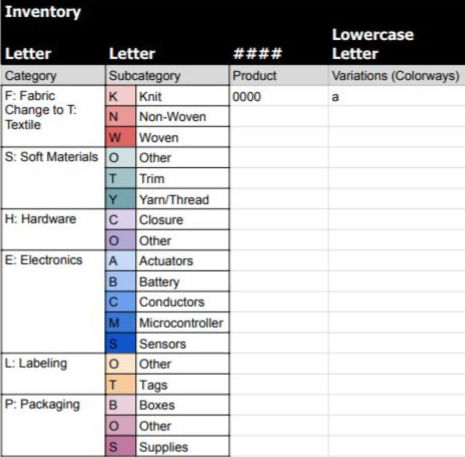

Electronics




Apparel


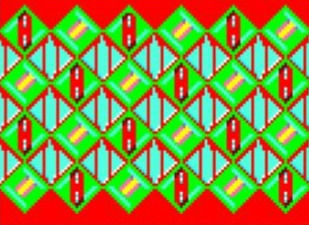

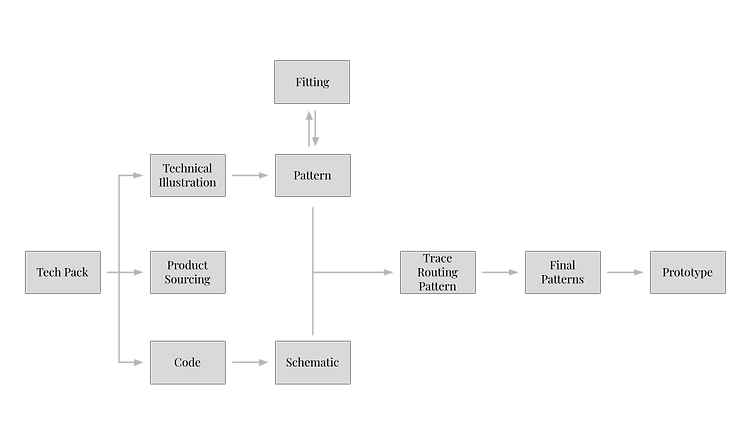_edited.png)
Integration
The integrated technical flat and trace routing pattern pieces are the connection between the apparel and electronic worlds. The integrated flat provides a relationship between the components of the garment. This helps to create the trace layouts and ultimately the final pattern.
When incorporating electronics into the tech flat it includes the shape of the component. It also shows the placement of the electronics in relation to the garment and body.
The trace routing pattern shown demonstrates all of the technical information of the piece. The next step is to mark the internal stitch lines and connection points to the electronics (center). This is used to make the final pattern (right). The stitch allowances are communicated in the construction sheet of the tech pack and the connection points are shown with the notches around the edges.

Trace Routing Pattern

Pattern Piece Draft
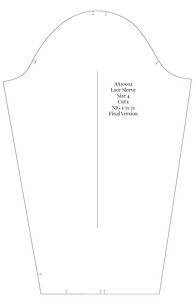
Final Pattern Piece

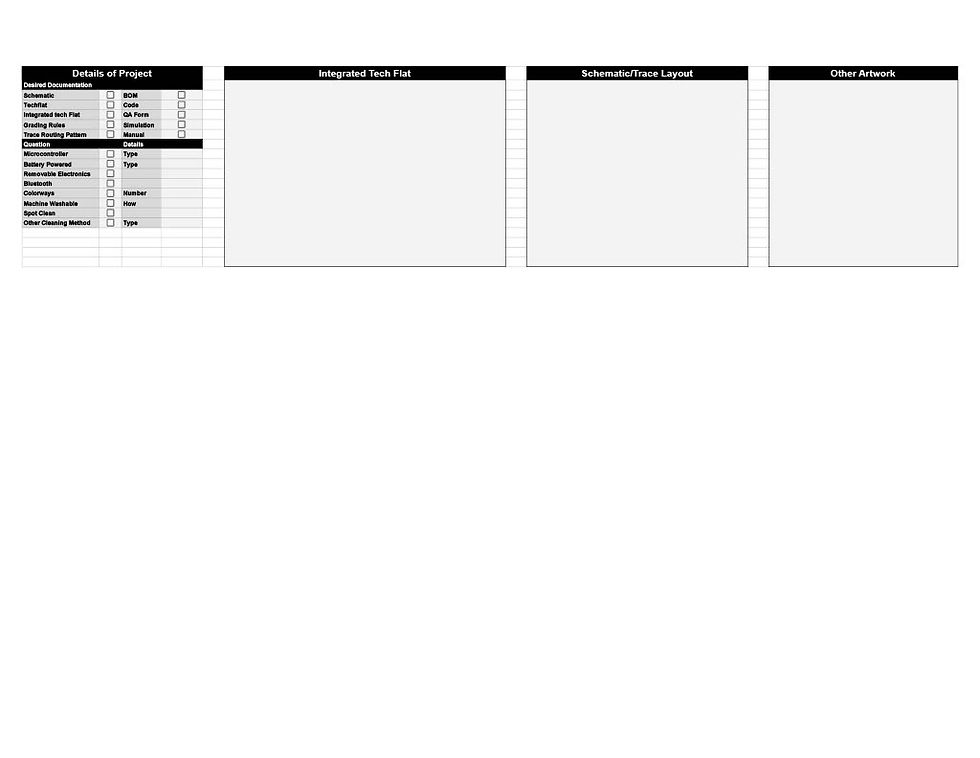
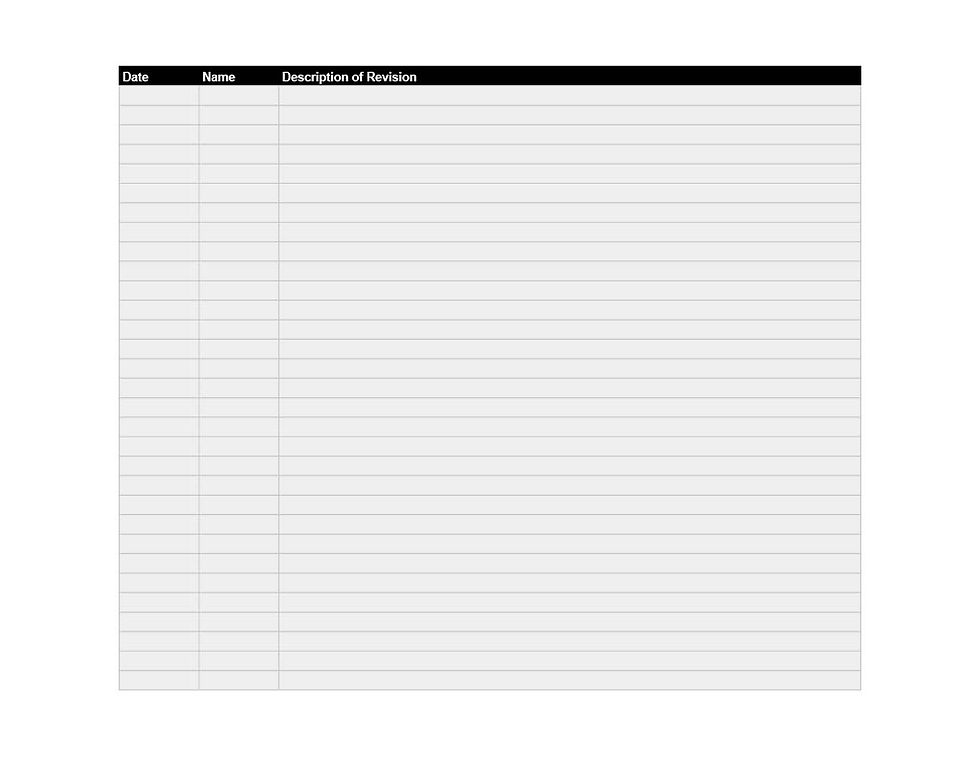

Tech Pack
As a manufacturer, one of the most important documents is the technical package (tech pack) also known in some companies as the specification sheet (spec sheet) or the dossier. The core content of the tech pack are the product summary, technical drawings, construction methods, fabrics and materials, labeling, and packaging information. Each company uses its own format, but consistency is key.
Case Studies
In-House Manufacturing
.jpg)
The first garment is an asymmetric burgundy dress with a pleated skirt and a motorized rotating flower on the shoulder. The garment has an attached earring that is a front for the pulse sensor. The pulse rate is connected to a vibrating motor in the shoulder that alerts the wearer if there is a sudden drop or spike, which may signify a larger issue.
This is a complex garment because it uses both conductive threads and wires. As of now, there aren’t wearable technology manufacturers that can produce garments like this at a small or large scale. As such, this garment has been chosen to be made in-house by Neshuma.
Communication Chain
_edited.png)
_edited.png)
Benefits
Chance to create a new system
Allows for more complex garments
Designers have more control on construction
Limits opportunities of miscommunication
Documentation



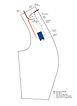
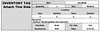
3rd Party Manufacturing
.jpg)
This garment performs a neuro-linguistic programming (NLP) technique called anchoring. Anchoring is a method of accessing thought and behaviour due to a sensory stimulus. In this garment the stimuli is a small vibrating motor sewn into the shoulder seam. The motor is activated by a small button in the cuff and is powered by a 3V battery, also located in the cuff.
In this case, the garment is being designed by Neshuma and is being produced by a third party manufacturer. For this case study, Neshuma has a handmade sample and is looking to start mass production.
Communication Chain
_edited.png)
_edited.png)
Benefits
Works within current manufacturing system
Single point of contact between Neshuma and the manufacturer allows all information to be confirmed
Limits cost on Neshuma for starting a business
Documentation





Separated Manufacturing
.jpg)
The final garment being produced is a women’s jacket to be worn over a gown. The jacket has an ultrasonic distance detector in the back which signals a vibration motor and LED on the cuff to alert the wearer if someone is within a set distance. This jacket provides the wearer with a sense of security as they walk to or from the event, whether to their car or all the way home.
The jacket is being produced as two separate components. First, the electronics are constructed and then they are shipped to the apparel manufacturer to be integrated into the rest of the jacket.
Communication Chain
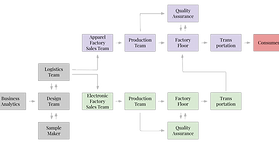
_edited.png)
Benefits
Allows for more complex garments to be prodiced
Fits into current system of manufacturing
Allows for the designers to access the full potential of the apparel and electronic industries
Documentation







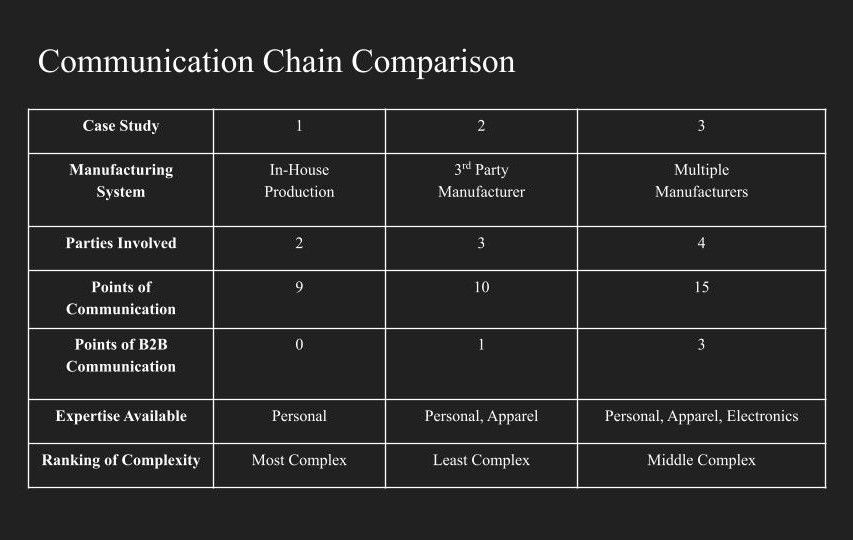


Discussion
These three case studies demonstrate different manufacturing methods for wearable technology garments. The three garments produced are a part of a line produced by the design firm Neshuma. Each product has been designed and tailored to the production method to which it belongs. With regards to the manufacturing system itself, each case study presents its own unique circumstances, benefits and constraints. The comparisons are visualized in the Table.